首先是由工人師傅根據(jù)經(jīng)驗進(jìn)行原料粗配、然后將配置好的原料投入到熔煉爐中加熱熔煉,達(dá)到一定時間后,取樣到光譜儀中檢測,光譜檢測的結(jié)果顯示了該熔液所含成分,工人師傅根據(jù)
裝配鑄鐵工作臺成品目標(biāo)值,判斷是否可以出爐,如果結(jié)果不合格,則需要人工計算精配原料重量,并由人工稱重加料,加熱熔煉后再次送至光譜儀檢驗,該過程直至光譜儀檢驗結(jié)果合格為止。
該生產(chǎn)過程中配料計算和稱重是 重要的環(huán)節(jié)。而傳統(tǒng)配料計算中由人工完成,要求技術(shù)人員具有較多經(jīng)驗,當(dāng)元素較復(fù)雜,原材料種類較多時,計算時間長、難度大、準(zhǔn)確度低。熔煉行業(yè)迫切需求一款能夠根據(jù)目標(biāo)成分要求智能化計算配料重量,并指導(dǎo)爐前操作的行業(yè)解決方案,達(dá)到質(zhì)量控制、成本 、流程可追溯的目的。但是,由于手工操作,
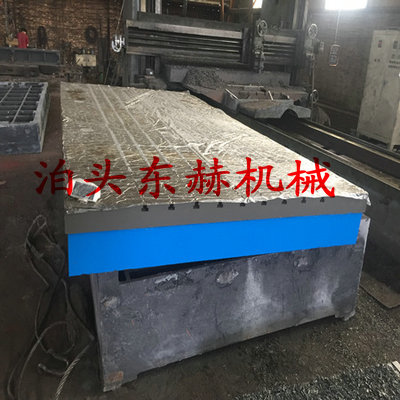
熔煉行業(yè)并沒有可以支持的生產(chǎn)數(shù)據(jù)。
我們基于百度的PaddlePaddle人工智能平臺對傳統(tǒng)熔煉行業(yè)進(jìn)行提升,以工藝知識+少量數(shù)據(jù)完成了127種合金鋼模型,生產(chǎn)過程中由模型自動計算原料的種類和重量,一次加料成功率高達(dá)95%以上。這種輕量化的工業(yè)智能顛覆了傳統(tǒng)熔煉過程中依賴人工經(jīng)驗、手工試算、估算添加的現(xiàn)狀,利用物聯(lián)網(wǎng)打通信息流、利用深度學(xué)習(xí)挖掘 模式、利用生產(chǎn)數(shù)據(jù)沉淀專家知識,有效避免了人為原因造成的用量不均、原料添加混亂等問題,快速、準(zhǔn)確地提供數(shù)據(jù)驅(qū)動的生產(chǎn)輔助決策,有效幫助企業(yè)提升質(zhì)量、降低成本、增產(chǎn)增效。 重要的是,隨著
裝配鑄鐵工作臺生產(chǎn)數(shù)據(jù)量的增量,工廠會形成屬于自己的生產(chǎn)模型,結(jié)果也會越來越準(zhǔn)確。