1.
焊接平臺型腔的尺寸不符合圖樣要求原因(1)型殼高溫強度低,其抗高溫變形能力也低。型殼變形大部分是在脫蠟、焙燒或澆注過程中產(chǎn)生的。澆注時,靠近澆口的高溫有可能使型殼發(fā)生變形。
(2)涂料的粘度大,涂層過厚,涂料堆積;或硬化液濃度低,溫度低,硬化時間短,硬化不足等原因,導(dǎo)致型殼的強度低。
(3)脫蠟液的溫度低,脫蠟時間太長。由于蠟料的熱膨脹系數(shù)大于型殼的熱膨脹系數(shù),脫蠟緩慢將導(dǎo)致型殼在脫蠟的過程中受到各種應(yīng)力的作用,是型殼在脫蠟過程中變形。
(4)中小件型殼的焙燒溫度過高、焙燒時間過長;或冷卻過快;或焙燒時擺放不當(dāng)(堆壓、擠壓),使得支撐受力不平衡等原因,引起局部變形。
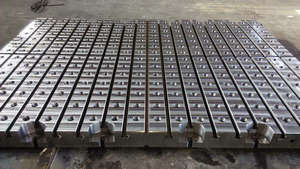
(5)焙燒爐不能滿足工藝要求。
(6)焙燒與澆注配合不當(dāng),型殼在焙燒后的熱態(tài)時,強度較高;溫度下降時,強度隨之下降。如型殼在冷態(tài)下澆注,型殼急劇升溫?zé)崤蛎浵禂?shù)大,導(dǎo)致型殼變形。
2.防止措施
(1)掌握、運用、控制涂料的“配比-粘度-溫度”關(guān)系曲線;注意涂掛操作,使涂層均勻地覆蓋;控制硬化液的濃度、溫度和硬化時間,使型殼充分硬化。
(2)型殼停放12~24h再脫蠟;選擇合理的脫蠟工藝,脫蠟液的溫度控制在95~98℃,脫蠟時間為15~20min,不超過30min;以及型殼在脫蠟過程中的擺放等。
(3)選擇合理的焙燒工藝,氯化銨硬化的型殼焙燒溫度T=850~900℃,時間0.5~2h;注意型殼在焙燒過程中的擺放,避免型殼彼此擠壓;控制焙燒出爐的冷卻速度等。焙燒良好的型殼呈白色、粉白色或粉紅色。
(4)加強焙燒爐的定期檢測和日常維護保養(yǎng),使其滿足焙燒工藝要求。